Welcome again Oracle Retail fans. This is the post which I'm sure you all must be waiting for. If you ever wanted to know all about Items, it's setup, usages etc, you are now at the right place. In this article, I'm going to talk all about Items. Please note that this post is a continuation of Oracle Retail Merchandising System Deep Dive article and if you are a beginner, you may want to visit Oracle Retail Merchandising System Overview article before proceeding on this article, however, it is not completely necessary.
Also, as mentioned in my earlier posts, this article covers each and every detail required for Item related questions in Oracle Retail Merchandising Systems (RMS) Certification (Pearson Vue Exam Number 1Z0-453) preparations.
So, here we go. In this article, we'll be discussing following details in depth, about Items in RMS Foundations:
1. Items
a. Item Levels/Hierarchy
b. Transaction Level Items
c. Item Number Types
2. Item Types
a. Regular Items
b. Pack Items
i. Simple Pack
ii. Complex Pack
iii. Vendor Pack
iv. Buyer Pack
v. Orderable Buyer Pack
vi. Sellable Packs
vii. Nested Packs
viii. Tracking Pack Stock On Hand
ix. Inner Packs, Case and Pallets
x. Other Pack Features
xi. Pack Summary
c. Deposit Items
d. Consignment & Concession Items
e. Transformable Items
f. Catch Weight Items
3. Item Ranging
4. Item/Supplier
5. Differentiators & its Usage
a. Diff Types
b. Diff Ids
c. Diff Groups
d. Diff Range
6. User Defined Attributes & Custom Flex Attributes
7. Seasons & Phases
8. Item Setup & Maintenance
9. Item List
10. Item Reclassifications
1. Items
The RMS item structure groups items together in what is commonly referred to as a ‘family structure’. RMS allows for up to three item levels within an item family. The naming of the item levels is a system level, user-defined setting. One level in an item family is identified as the transaction level. All of the items in the same item family must have the same transaction level. The terms ‘grandparent’, ‘parent’ and ‘child’ are sometimes used to discuss the relationships between the different item levels. All items, regardless of entry method, will follow this type of structure. This is further discussed in the Item Levels section below.
1.1 Item Levels
Items can be grouped into a one level family, a two level family, or a three level family. The naming conventions that are used for the 3 levels in RMS are below:
· Product (grandparent of UPC and parent of SKU, also known as Level 1)
· SKU (parent of UPC and child of Product, also known as Level 2 or Transaction Level)
· UPC (child of SKU and grandchild of Product, also known as Level 3)
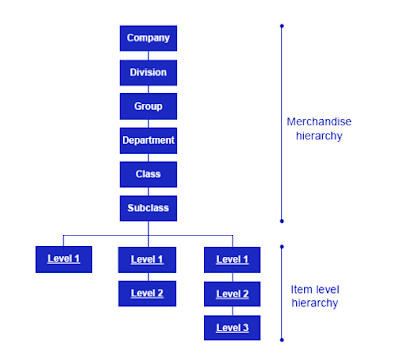
Level 1
Commonly referred to as a ‘Product’ or the ‘Grandparent’ (in a 3 level group structure) is the level, above which level 2 items (i.e. SKUs) exist. In a fashion context, the level 1 item may be “SS Twisted Neckline”.
Level 2
Commonly referred to as the ‘SKU’ level or the Transaction Level, this is the level at which goods are transacted in a 3 level hierarchy (packs not included). This is the level at which inventory is held, orders are raised and transfers/allocations/sales/returns/adjustments are transacted. This also allsows pricing colors and sizes differently within the same item family.
Level 3
The third item in the 3 level item grouping in RMS refers to the reference item. This level will be used to store the reference items associated to an SKU. It is possible to assign multiple reference items of the same type or different types to an SKU, e.g. UCC, UPC, EAN, ISBN, and PLU. It should be noted that the same reference item cannot be assigned to two different SKUs in RMS at the same time. Typically, this is the level at which a barcode is assigned to the item. A barcode is the industry standard numbering system, which uniquely identifies a product when scanned. An item may have multiple barcodes associated with it (due to sourcing from multiple suppliers etc.).
See example below of a 3 level item structure for the “SS Twisted Neckline”:
1.2 Transaction Level
For every item family in RMS, one of the levels is designated as the Transaction Level. This is the level in which all transactions/stock movements (PO, Receiving, Allocations, Shipments, Sales, and Pricing etc.) are tracked.
Below is a table describing in further detail, the functions available at/above/below the transaction level:
Following is the high-level item setup flow:
1.3 Item Number Types
Following is the quick summary of the different type of Item Sequencing Numbers that can be used in RMS:
2. Item Types
There are several different types of items you can create in RMS. Let's understand each.
a. Regular Items
b. Pack Items
i. Simple Pack
ii. Complex Pack
iii. Vendor Pack
iv. Buyer Pack
v. Orderable Buyer Pack
vi. Sellable Packs
vii. Nested Packs
c. Deposit Items
d. Consignment & Concession Items
e. Transformable Items
f. Catch Weight Items
2.1 Regular items
In simple term, a Regular Item is an item with no additional specific attributes like (packs, deposits, consignment etc). User needs to select Item Type as “Regular Item” in order to create a regular item.
2.2 Pack Items
RMS supports the creation of pack items. A pack is a group of items that are sold and/or ordered as one item. By grouping individual items together to make an item, the buyer can order by the pack instead of selecting the single items and quantities.The pack is assigned its own item number and similar to a non-pack item. The components of a pack with their associated quantity in the pack are stored as well – this will allow the RMS applications to track the inventory of the component items when a pack is processed in an inventory transaction. A pack item is also created on the po screen and children will automatically be created when a pack item is set up.
Different types of packs can be set up; simple and complex packs.
1. Simple Pack
Simple packs contain multiple units of one SKU. A simple pack is always orderable. You can make the pack sellable. A simple pack is an orderable vendor pack with multiples of one the same component item.
Consider below business case for Retailer:
A Simple Pack is an orderable (and optionally sellable) vendor pack item that contains multiples of one item. It allows Retailer to replenish an item by actually ordering packs of the item (e.g. case of 24, case of 12, case of 6) instead of the individual item itself. An item (component item) can be associated to one or more Simple Packs
Example:
When creating a simple pack for a component item, you must provide the following information:
· Type of number, pack number, and pack description
· Number of units of the component item that make up the pack
· Primary supplier and country of sourcing for the pack
· Unit cost of the pack
· Number of packs in a case, cases on a tier, and tiers on a pallet
· Base retail price of the pack if it is sellable as a pack
In addition, you can define the dimensions, weights, and volumes of cases and pallets. After defining the attributes of the pack, you can choose to copy other details from the component item. The details may include suppliers, stores, warehouses, seasons, user defined attributes, ticketing, required documents, sales taxes, HTS numbers, and expenses.
Simple Pack Setup Window:
2. Complex Pack
Complex packs can contain a Product with multiple items (within the same Product/color and across colors within the Product) with one or more units for each item or multiple Products which contain one or more units for each item.
Other pack attributes that can be assigned to either a complex or simple pack include the following:
· Vendor pack – a pack defined by the supplier whereby the cost/retail may or may not equal the sum of the cost/retail of the component items. Both Complex and Simple Packs can be Vendor Packs.
· Buyer pack – a pack defined by the retailer, generally used to ease the ordering process with the cost/retail equaling the sum of the cost/retail of the component items. Only Complex Packs can be Buyer Packs.
· Sellable pack – a pack that can be sold with its own retail that may or may not be equal to the sum of the items in the pack.
· Orderable pack – a pack that can be ordered with its own cost that may or may not be equal to the sum of the items in the pack.
3. Vendor Pack
Some vendors prefer to dictate the contents of the “pack”. If a pack is created by the vendor it will always be “orderable”, but not necessarily “sellable”. Since the pack has been defined by the vendor, RMS will always order and receive it as a pack. It cannot be broken down to the component or SKU level. The unit cost will default on pack creation to the sum of the component’s costs (as with buyer packs), but can be edited. The unit cost will not be updated if items are added or deleted or if an item’s unit cost for the primary supplier has been changed. The cost change must be created if it is desired that the unit cost for the vendor pack reflects a change in a component’ cost.
· Contents dictated by the Vendor
· Always Orderable
· May or may not be Sellable
· Always ordered & received as a Pack in the warehouse. May be exploded to the component after receipt in the store.
· Pack Unit Cost defaults to sum of the unit cost components times the quantity of each component, but may be edited
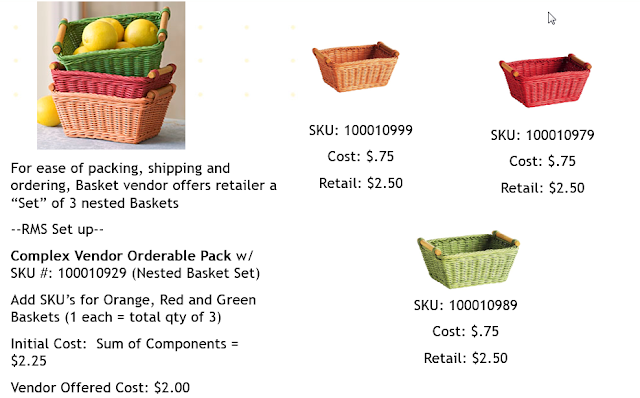
When a pack is “orderable”, then the user must assign a supplier. Therefore, each component of the pack must be supplied by that supplier. If the orderable pack contains a non-orderable inner pack, the inner pack’s components must be available from all the suppliers of the outer pack. If department level ordering is turned on in the system, during the ordering process, when using a buyer pack that is orderable as Eaches, the component’s department must be the same as the Pack Item’s department.
Also, all orderable packs can be inventoried in a warehouse at the pack level. Breaking of packs can occur at the warehouse so that a pack can be reduced down to the inner pack or SKU levels. Once broken, the pack cannot be rebuilt again as a pack item. (Select Pack Items/Break Pack from the Inventory menu).
It is possible to transfer an orderable pack from a warehouse to a warehouse and from a warehouse to a store. Otherwise, transfer will take place at the style or sku level.
4. Buyer Pack
As the name defines, the source of the buyer pack is the buyer. The buyer pack can be orderable and/or sellable. If it is orderable, the buyer still has the option of ordering and/or received as eaches or a pack. A Pack can also include other packs as its content. The pack unit cost will be calculated from the sum of the unit cost times the quantities of each item in the pack. Unit cost is obtained from each item’s primary supplier. Also note that any price change to the components of the pack will be updated in the calculation of the pack unit cost.
· Created by the buyer
· May be Orderable and/or Sellable.
o If Orderable, may be ordered/received as eaches or as a pack
· Pack Unit Cost = sum of the unit cost components times the quantity of each component
Buyer Pack Setup Example
5. Orderable Buyer Pack Items
· Multiple items to streamline ordering
· Created by retailer
· If supplier does not recognize pack, it must be exploded to components at ordering
· No cost advantage
· Different items or multiples of the same
· Cost = sum of components
· Same Supplier/Origin Country
· Components can be from any department
6. Orderable Vendor Pack Items
· Multiple items ordered as one
· “Created” by vendor
· Cost savings to retailer
· Can contain different items or multiples of the same item
· Cost can be different to the cost sum
· All components must be available from the same Supplier/Origin country
· Components can be from any department
· Must be ordered as a pack.
· Vendor determines components.
7. Sellable Pack Items
Sellable Packs are the packs that are eligible for the sale at the Stores. It is sold as one item. Sellable Pack Item Stock On Hand can be viewed at Store Level in Store Inventory management (SIM). RMS only has visibility to the Component SOH.
· Multiple component items
· Sold as one item
· Offers price discount over total price of components
· Component items can be from different departments
· Component items can be from multiple suppliers/origin countries
8. Nested Packs
Retek allows users to have packs within packs. However, the system is limited to two levels of pack hierarchies. A pack may be broken down to its inner pack and/or component level (Fashion/Staple Sku) to adjust the stock on hand for both the Pack item and the components at the warehouse. Once the pack is broken down, it may not be built back up again into a pack item. At the time the pack item is broken down at the warehouse level, it is assumed that the components at the warehouse are not in deleted status. Nested Packs require breaking twice -- once to the Inner Pack level -- again to the Component level.
Example: Buyer creates a pack of suit jackets, another pack of suit pants, and the third pack of suit skirts. Then, the buyer creates an outer pack containing combinations of the three Inner Packs of jackets, pants, and skirts
9. Tracking Pack Stock On Hand
The stock on hand of a Pack item is tracked at the warehouse, but not at the store. When received at the store, the inventory is broken down into the individual components of the Pack Item.
RMS does allow the user to access “stock on hand” for a pack at store level through Inventory/Pack Item/Build Sellable Pack. This is only available for sellable packs.
• In RMS:
– Pack on hand is only visible at the warehouse level (for orderable packs only)
– Pack on order visible at DC and Store level
– Once RIB sends message to RMS that an item was received at the store, RMS always shows SOH at the component level
• In RWMS:
– If ordered as pack, on hand is always tracked at pack item level
• In Store Inventory Management:
– If orderable (not sellable), on hand (OH) is tracked at component level
– If Orderable/Sellable, SIM initially tracks the OH at the pack level based on the number of packs received. Inventory adjustments can be made at store level to break packs into component items whereby OH can be tracked for both the pack and the components.
• Visibility to potential store on hand available through “Build Sellable Pack” function which uses the on hand of the components to determine the maximum number of packs available to sell
10. Inner Pack, Case and Pallets
Inner Pack: Inner pack (or Shelf pack) is a sub package within a master carton or a case. Normally this is some shrink-wrapped or bundled quantity of retail units within a case. The inner pack is made up of one or many retail units. This is typically used as a handling unit during piece-picking operations in warehouses and other supply chain processes. If set to greater than 1, a store order is fulfilled in multiples of an inner.
Case: A case is composed of a certain no. of loose units or units bound together as inners. The case serves to lessen material handling time and adds protection during shipping to the inner packs. Quantities are typically ordered and shipped in terms of cases.
If a Supplier produces a package of 3 selling units (SKU’s) T shirts in each Inner pack and in a Case, there are 4 Inner packs (containing 3 SKUs each) , thus there are 12 SKUs in a Case.
Pallet: A pallet is a flat transport structure that supports goods in a stable fashion while being lifted by a forklift, pallet jack or other jacking device. A pallet is the structural foundation of a unit load which allows handling and storage efficiencies. Goods or cartons are often placed on a pallet secured with stretch wrap or shrink wrap and shipped.
Example::
11. Other Pack Features
RMS also supports the use of Deals, Brackets and Allowances (D,B,A’s) for pack items. If the pack item is a vendor pack, the D,B,A’s will be based on the Pack item and applied to the unit cost of the vendor pack. If the pack item is a buyer pack, by definition, the pack’s unit cost is just a sum of the unit costs multiplied by the quantities of the Staple/Fashion Sku’s with in the pack. Therefore, the D,B,A’s will be determined by the component sku’s potential discounts and applied to the unit costs of the component Staple/Fashion Sku’s to determine a total D,B discount or allowance for the buyer pack.
The OTB will be adjusted at the component sku’s department, class, subclass level regardless of the pack item’s merchandise hierarchy. RMS also allows pack level Returns to Vendor if the pack fails Quality Control
12. Pack Summary
2.3 Deposit Items
A deposit item is an item that has a portion which is returnable by the customer after it has been sold to the customer. A deposit is taken from the customer for the returnable portion. A deposit item is broken into the components of the item, and each item is tracked separately in RMS.
· Deposit Contents Item: The item that is sold to the customer.
· Deposit Container Item: The item for which the deposit is taken. The deposit container item holds the deposit contents item.
· Deposit Crate Item: The item which holds the container and contents items.
· Deposit Returned Item: The item that is returned to the retailer by the customer and for which the deposit is returned to the customer.
A deposit item:
· Allow content items (e.g. liquid) to be linked to their associated container item (e.g. bottle).
· Facilities added to ensure a 1:1 relationship between content and container items for POs and RTVs.
· The ability to replenish complex pack items containing both content and container items as well as a crate item.
· Visibility to a pack’s component item breakdown within the ordering dialog.
2.4 Consignment and Concession items
2.4.1 Consignment Items
Let’s first try to understand what Consignment Is. A great article written on this by Dave Piasecki. Some of the excerpts mentioned below are referred from his article (with my few additional cents) which explains consignment inventory details like no other.
Consignment Inventory is inventory that is in the possession of the Retailer, but is still owned by the supplier.
In other words, the supplier places some of his inventory in Retailer’s possession (in their store or warehouse) and allows them to sell or consume directly from his stock. Retailer purchases the inventory only after he has resold or consumed it.
The key benefit to the Retailer should be obvious; he does not have to tie up his capital in inventory. This does not mean that there are no inventory carrying costs for the Retailer; he does still incur costs related to storing and managing the inventory. So what’s in it for the supplier? This is where the benefits may not be so obvious—or may not even exist. Let’s start with a classic consignment model that has significant benefits for the supplier.
Where Consignment Works Best.
A supplier has a product or group of products that he believes will sell if he can get them in front of end-users. The trick is that getting them in front of end-customers means getting them stocked in retail establishments. Retailers are hesitant to stock the product because they do not have the same level of confidence in it as the supplier, they do not want to invest the money and risk getting stuck with something that may not sell. Because the supplier realizes in-store exposure is critical to getting his products sold, he offers to stock his product in their stores. This creates a condition of shared risk whereby the supplier risks the capital investment associated with the inventory while the customer risks dedicating retail space to the product. This also creates a condition of shared benefit because neither the supplier nor the customer will benefit until the product is sold to an end-customer. This shared-risk/shared-benefit condition will often be enough to convince a Retailer to stock the product.
For a more specific example, consider a bicycle manufacturer that produces a wide range of bicycles ranging in price from a couple hundred dollars to several thousand dollars. He has Retailers (local independent bicycle shops) that stock his low-to-mid-priced models but are hesitant to stock the more expensive bikes because they do not have the confidence that their customers are willing to pay that much for a bike. And, if they do get a customer that wants a high-end bike, they could always special order it for them. The bicycle manufacturer strongly believes that getting his high-end bikes in the shops where customers can see and touch them is critical in driving up sales for these models as well as helping to promote his brand which ultimately drives up sales for the lower cost models. The solution? Well I think you can take it from here.
Consignment model works well for:
· New and unproven products
· The introduction of existing product lines into new sales channels.
· Very expensive products where sales are questionable.
The key to all these examples is the combination of a high-degree of demand uncertainty from the customer’s point of view, and a high degree of confidence in the sales potential from the supplier’s point of view. The consignment inventory model can also be effective with service parts for critical equipment where the customer would not stock certain service parts due to budget constraints or demand uncertainty. In this situation, consignment inventory allows the supplier to provide a higher service level (by having the parts immediately available), save expedited freight costs, and ensure the customer does not procure a replacement part from a competitor.
2.4.2 Concession Items
A concession item is similar to a consignment item in that the retailer does not own the inventory being sold. Concession items differ from consignment in that the ownership is not transferred when the items are sold. A retailer rents floor space to a supplier on which the supplier sells their goods. A record of concession sales is recorded and the retailer then bills the supplier using their chosen method.
2.4.3 Difference between Consignment and Concession items
Concession Items are similar to consignment but differ in the way sales are processed.
Consignment
|
Concession
|
Purchase Orders generated for sold items.
|
No POs generated for sold items.
|
Invoice documents are created for sold items.
|
No invoice documents created for sold items.
|
Purchases will be recorded on stock ledger.
|
No impact to stock ledger.
|
The consignment rate can be changed temporarily via a promotion.
|
The concession rate cannot be temporarily change.
|
No Accounts Receivable and Payable records are recorded.
|
Accounts Receivable and Payable records are recorded for the item/supplier/calendar period.
|
2.5 Transformable items
A transformable item is an item that can be ordered as one item and the broken into smaller items. The smaller items can then be resold in the store. There are two types of transformable items:
· Transformed Orderable: The item is ordered from the supplier in one form, but changed by the retail and sold to the customer in a different form.
· Transformed Sellable: The item that is sold to the customer. A transformed sellable item is ordered from the supplier in a different form than it is sold.
If you are creating a transformed orderable item, you will not be able to select the Retail by Zone option from the options list. If you are creating a transformed sellable item, you will not be able to select the Supplier option from the options list. Retailers, particularly grocers, may require the ability to order an item and have it broken down into multiple sellable items.
You may change one item to a second item or you may consolidate multiple items into one item. Items are transformed at a finishing location. There are certain conditions that must be met before you complete and item transformation. When you transform the first item into a second item, the second item must exist in approved status in the merchandising system before you can complete the transformation. The entire quantity of item on a transfer must be transformed to the same item.
There are two types of item transformation that can occur:
Transformation Type
|
Source Item
|
Transformed Item
|
One to one
|
Item A
|
Item X
|
Item B
|
Item Y
|
Item C
|
Item Z
|
Many to one
|
Item A
|
Item X
|
Item B
|
Item C
|
2.6 Catch Weight Items
· Catch Weight functionality allows items that may be purchased and sold in varying weights to be better managed within RMS.
· An item’s cost can now be managed in a unit of measure that differs from the item’s standard unit of measure.
· An average weight per unit will be maintained for a simple pack at a receiving warehouse.
· Purchase in Fixed Weight Simple Packs, Sell by Variable Weight. For example, Bananas.
· Purchase in Variable Weight Simple Packs, Sell by Variable Weight. For example, Deli Meat.
· Purchase in Fixed Weight Simple Packs Containing a Fixed Number of Eaches, Sell by Variable Weight Eaches. For example, Pre-Packaged Cheese.
· Purchase in Variable Weight Simple Packs Containing a Fixed Number of Eaches, Sell by Variable Weight Eaches. For example, Pre-Packaged Steak.
3. Item Ranging
As part of item set up, the item will be ranged to a subset of initial locations which have been identified to be all warehouses and the e-commerce store. At the item location level, the status of that item can be maintained to control various functions.
These functions include the following:
· Active – The item is valid and can be ordered and sold.
· Discontinued – The item is valid and sellable but no longer orderable.
· Inactive – The item is valid but cannot be ordered or sold.
· Deleted – The item is invalid and cannot be ordered or sold. Note that setting item-location to this status will not result in the actual deletion of the location from the item.
If an item can no longer be ordered to a location, the item-location status can be changed to Inactive. If an entire item can no longer be ordered, the status at all locations for the item can be changed to Inactive using the Mass Update Item-Location Change dialog. An item list can also have its item-location status changed for all item-locations in that item list.
4. Item/supplier
RMS allows for multiple suppliers of the same item. In this case, one of the suppliers must be designated as the primary supplier of the item. This functionality also allows for different costs and retails by the supplier for the same item. From an item numbering perspective, the Level 1 Product number and the Level 2 SKU number will be the same for each item supplier combination. The Level 3 UPC numbers will be different based on the supplier or suppliers. Please see the diagram below for an example:
In RMS, once the item is received at the Warehouse, there is no differentiation between items supplied by different suppliers. This configuration is a customer facing configuration because a customer at the store cannot distinguish the same items from more than one supplier. Inventory and Sales are tracked at the Level 2 SKU level and not by Item-Supplier level.
Item Supplier relationship is by item, supplier, country, and location level.
· The cost of an item can vary by location from a Supplier, therefore, the Client can specify a primary supplier and primary country by location and maintain cost at that level
· This recognizes a supplier’s ability to source an item from multiple countries and manage cost by locations.
· All items require one Primary Supplier
· Location Default & Case Information:
o When “Unit Cost” is entered, RMS will calculate the Case Cost based on Case information entered.
o When “Case Cost” is entered, RMS will calculate the Unit Cost based on case information entered.
· Supplier lead time can be defaulted from the Supplier to the Item/Supplier/Country level.
· Pick up lead time - lead time if the retailer picks up the truck from the supplier and delivers it to the warehouse.
· Dimensions may also be specified for an each, inner, case, and pallet. This will allow item dimensions to be used:
o For the interface to a space management system.
o For rounding within RMS.
· Tare Type and Tare Weight allow a retailer to separate out the packaging weight from the product weight. Used only for grocery.
· Statistical Case can be specified for supplier minimums and scaling, this is the cube dimensions of a pack and can be used in to determine packing capacity.
· Liquid volume – Liquid unit of measure
· Presentation Method field can be interfaced to a presentation system for presentation on a Plano gram.
5. Differentiators and its Usage
5.1 Differentiators Detail
In RMS there are 4 major Diff Groupings:
Diff Types – the highest diff grouping level
· Example: Color, Size, Flavor
· Maximum Diff Types allowed in RMS: 30
· Diff Types may be chosen per Item.
Diff IDs – primary component of diff types
· Diff IDs are assigned to Diff Types
· Example: Diff Type of “Color” includes Diff Id’s “Blue”, “Red”, “Black”, “Pink”, “Yellow”
Diff Group – used to logically group Diff Ids within a Diff Type
· Attached to level 1 items to create level 2 items
· Example: Diff Type of “Color” includes Diff Id’s “Blue”, “Red”, “Black”, “Pink”, “Yellow” where only “Pink” and “Yellow” are included in a Diff Group called “Spring Colors”
Diff Range – a subset of the diff group
· Primarily used to streamline ordering the most frequently ordered sizes within a diff group
· Example: A color Diff Group might have 20 colors, but 4 are bought more frequently. A Diff Range of those 4 colors could be attached to the diff group and the range is used during ordering or item creation
Diff groups are attached to an Item. The diffs in the diff group define the full range of choices that the SKU and the item can have.
An example of Diff Structure is shown below.
Diff Summary
5.2 Setup & Maintain Diffs
Add a Diff Type
Navigate: From the Main Menu, select Items > Diffs > Diff Types > Edit. The Diff Type. Maintenance window opens.
Maintain Diffs
Navigate: From the main menu, select Items > Diffs > Diff IDs > Edit. The Diff ID Maintenance window opens.
Create/Copy a Diff Range
Navigate: From the main menu, select Items > Diffs > Diff Range > New. The Diff Range Maintenance window opens.
Create a Diff Ratio
Navigate: From the main menu, select Control > Diff Ratios. The Diff Ratio Find window opens.
6. User Defined Attributes (UDA) and Custom Flex Attributes (CFA)
6.1 User Defined Attributes (UDA)
User Defined Attributes (UDAs) are used within RMS to capture additional characteristics of an item to allow for reporting or grouping purposes. UDAs can be used as criteria to build item lists. Mass updates to items can be made using UDAs as well. UDAs can be assigned at different levels of the merchandise hierarchy; namely department, class, or subclass, which then can be defaulted to the item level.
UDAs are used to define characteristic of an Item in a better way. This can be defined by an user at any time and anywhere in the merchandise hierarchy, right from ‘Department’ to the last level of the item. These can be made a mandatory or an option field. UDAs do not have any impact on any other modules of RMS. They can be used as a medium of conveying a message to the different departments within the organization or to a vendor. For Ex: A retailer can inform his supplier on what kind of packing is required for one particular item.
In RMS, there are 3 types of UDAs.
· List of values
· Free from text
· Date
To use UDAs effectively, you must first add the UDAs to the system. You can then add UDAs to a department, class, subclass, item, or item list. Alternatively, you can add departments, classes, subclasses, or items to a UDA.
6.1 Custom Flex Attributes (CFA)
Custom Flex Attributes (CFAs) are additional attributes for items. The main difference between UDAs and CFAs is that UDAs have functionality within RMS; CFAs do not. CFA’s are created within RMS but are staged to be interfaced to external systems. These attributes can be viewed under the Item, Item/Location, Item/Supplier, Item/Supplier/Country, and Item/Suppler/Country/Location forms.
7. Seasons and Phases
A season is a specific selling period during the year, and a phase is a smaller time period within a season. The start and end date of a phase must be within the start and end date of the season. There can be more than one season and phase for an item. Seasons and phases can be criteria to build an item list and can be used for reporting purposes. The season and phase data can be attached at the product level (level 1 item) and then default to all the SKUs (level 2 items).
· Seasons: Associate an item with a particular selling period during a year.
· Phases: Smaller periods within a Season
Creating New Season/Phase
Adding Season/Phases to the Item
8. Item Tickets
A ticket is a tag that is affixed to an item in the store. The purpose of the ticket is to carry information on the item that cannot be usually depicted on the product. A ticket contains important information about the product. Information like the item code, price of the product, particular instructions for handling the product, etc. In RMS the ticketing functionality allows the retailer to specify the type of information the ticket should contain as regards the product.
- Allows multiple tickets per item.
- Allows user to determine when to print and the quantity of tickets.
- Supports manual ticket requests.
- Nightly batch job extracts ticket request to the external printing system.
The setting of the format of the ticket or making the ticket type as well as manual initiation of requisitioning a ticket happens in RMS. While the actual printing of the tickets is done by an external application viz; Avery or GXS. A ticket type in RMS broadly defining the characteristics of a ticket according to the nature of the information it contains, and the nature of the item it is meant to get affixed on. Individual items can be associated to tickets through the Request Ticket window in RMS. Multiple items are associated with the help of an item list or a Purchase order through the same window.
In RMS there is provision for mentioning the circumstances under which a ticket can be automatically printed for an item. This is when the item is associated with a purchase order. Tickets can be automatically printed under 3 circumstances in RMS.
- On the approval of a Purchase Order
- On the receipt of a Purchase Order
- When a permanent price change is effected
We must have to mention whether we choose to initiate automatic printing of tickets either at approval or receipt of a purchase order. Only one option can be chosen. We can though, simultaneously alert whether we need auto printing in case of a price change along with the purchase order ticketing stipulations. When Price Changes are approved in RPM, they are published to RMS to generate the ticket request for the specified item/location. Promotions and clearance events are communicated to RMS for the purpose of ticketing. System also allows us to specify in percentage the number of tickets we want to be printed over and above the number of items in the PO. By default, we have 5% which we can alter to our choice if we so wish it.
Setting up Tickets:
Adding Tickets to the Item:
The TCKTDNLD.PC program creates an output file containing all of the information to be printed on a ticket or label for a particular item/location. This program is driven by the “requests” for tickets that exist on the TICKET_REQUEST table. Information to be printed on the ticket is then retrieved based on the item, location and the ticket type requested. The details, which should be printed on each type of ticket, are kept on the TICKET_TYPE_DETAIL table.
9. Item Setup & Maintenance
It is important to understand the different color conventions for the left navigation on Item Master Form, before setting up the item.
· Red – The option is required, but has not yet been completed.
· Green – The option is not mandatory but has been edited.
· Bold Green – The option is required and has been completed.
· Blue – The option is available, but not required.
· Black – The option is not available given various constraints on the record.
· Grey - The option is not available for the selected item type/attribute.
The Item Master Form in RMS follows left-to-right, top-to-bottom sequence with some additional navigations available on the left-hand side. Below is an ideal sequence (not always necessary, if you are an expert) for setting up different types of item:
10. Item List
An Item List is a group of items and can contain Products, SKUs, reference items and packs. Item Lists allow the user to be more efficient when performing maintenance in RMS and they can be used throughout many Oracle Retail applications. Item Lists can be used in such processes as the following:
· Generating retail price changes, promotions, and clearances
· Reclassifications
· Generating cost changes
Note: When creating an Item List for a Cost Change all items included in the list must have the same supplier. Costs can be different per item-supplier relationship.
When creating an item list, the user has the ability to create the list as either static or dynamic. A static item list is where the items on the list remain fixed and must be maintained manually by the user. A dynamic item list is built based on a criteria specified by the user and can be re-built at any time using this criteria (i.e., as an item meets the criteria it is added to the item list). Dynamic item lists are manually rebuilt and not automatically updated.
In creating an item list, the user also has the ability to nominate who can maintain the list. The User Security Indicator function determines whether or not one or more people can maintain the item list. If the User Security Indicator is checked, then only the creator of the item list has the authority to maintain it. If the User Security Indicator is not checked, then anyone having access to the Item list can maintain the list. Regardless of the User Security setting, anyone can use the item list.
Items can be added to an item list by individually selecting the Product, SKU, reference item or pack item or by selecting the items using criteria. Using criteria to build item lists helps ensure data integrity. Available criteria options include:
· Merchandise Type (Product, SKU, UPC)
· Merchandise Hierarchy (department, class and/or subclass)
· Supplier
· Diffs
· UDA and values
The item list feature allows you to create, copy, edit, view, and use a group of items that are identified by one ID.
Create an Item List
Add an Item List/Location List Link
Add Items to an Item List
11. Item Reclassifications
Item reclassification allows moving an item or item list from one department/class/subclass to another. Reclassification can be done for a staple SKU, fashion style, pack item, or a list of items.
· An effective date can be specified for the reclassification. The actual process is done the night before the effective date
· Some of the checks done before an item can be put on a reclassification are as follows
· RMS will check to see if the item has the UDA (User Defined Attributes) that is required for the new Merchandise hierarchy, if it does not the item will be rejected.
· RMS will check to see if the item has default UDA's, if it does not, it will still reclassify the item but, a warning message will be written to a report.
· If the item is on any not-yet-processed "unit and value" stock count. If it is, it can not be reclassified.
· If the item is part of a consignment department and it is being reclassified to a non-consignment department and vice versa reclassification fails.
· If the item is forecastable, RMS will check to ensure the new merchandise hierarchy has a domain in Retail Demand Forecasting (RDF). If a domain is not associated with the new merchandise hierarchy, the reclassification will be rejected. If there is a domain change in RDF, RMS will write all store sales history for the item to the forecasting download.
· The item exists in another reclassification event.
· If the item level of the item is not equal to 1, then it cannot be reclassified. .
· One or more items on the reclassification event exist on approved partially received orders.
· If item is in a simple pack, it will fail reclassification. The item can only be reclassified along with its component item.
· If item is a pack item, it cannot be reclassified from merchandise to consignment department.
· When an item is successfully reclassified
o Sales history: A reclassification event does not rebuild sales history automatically. A reclassification does not affect previously recorded sales history. RMS maintains three levels of rolled up sales history: department, class, and subclass.
o Stock ledger: Stock ledger transactions are written to move the inventory amount associated with an item from the old department, class, and subclass to the new. Existing stock ledger transactions are not updated to reflect the hierarchy change.
o Open to buy: Open to buy (OTB) records are updated for all orders that are approved, but have not yet been received.
o Forecasts: If the reclassified item is forecastable and the new hierarchy values move the item to a new forecast domain, then an indicator is reset for the item at the item/store level. This change indicates to the program responsible for extracting sales history that the next time sales history is extracted from RMS for that item and store combination, all sales history should be extracted. Normally, only the sales history that occurred since the last data export is extracted.
12. Summary Note
Did I miss any topic with respect RMS Items? Please do let me know. I’ll try to cover. Items functionality in RMS is not just a huge but also a complex functionality. I hope this article will try to help on understanding all about that.
13 comments :
It is a very good post, compare epos suppliers uk and found it be really helpful information.
Thank you for writing such a nice blog with useful information. I hope you will share some more info about Inventory Buyers Overstock Buyers Closeout Buyers Wholesale Liquidation Company
The towing business is considering high-quality times these days. Buying used tow trucks is a high-quality idea as they will be cheaper and this way you don´t need to spend a group on them. Previous to you buy one, decide which type you would want to add to your tow company. Make sure you have the needs in mind earlier than you go look for them. Since the number of vehicles on the road is increasing day by day, towing commerce will see nothing but positive growth.
Thanks
Retail truck
Beauty truck
Business on wheels
Find details of companies Supplying Steel Furniture, Manufacturing & wholesaling metal crafted furniture in India. Get Steel Furniture at best price from Steel Furniture Retailers, sellers, traders, exporters & wholesalers listed at
Home Decorations Manufacturers
Baby Care Products Manufacturers
household items manufacturers
dairy products manufacturers
Wholesale Liquidation Company - Merchandise USA is your trusted source of wholesale liquidators.
Great piece of information, Thank you for sharing the updated one...
landlord furniture packs
Furniture packages
Thanks for sharing this useful blog list. This makes us easier to find the blog we need.
Well Done.. I admire the value you have provided through the web.. This will for sure going to be helpflul for all..If you are small firm lookking for the accounting and bookkeeping services , here are my services listed below:
bookkeeping services
Online bookkeeping services
Hey, nice site you have here! Keep up the excellent work!
Furniture Pack
landlord furniture packs
Useful Information, Thank you for sharing these, its so helpful.
landlord furniture packages
Furniture packages
Thank you for sharing us this awareness, Grateful.
Furniture packages
Good blog post Retail Audit Image Recognition
Retail inventory tracking softwareis a game-changer for managing stock efficiently. It offers real-time data, integrates seamlessly with POS and e-commerce systems, and provides valuable insights through advanced analytics. This helps retailers optimize inventory levels, reduce costs, and enhance customer satisfaction. Investing in such software streamlines operations and supports smarter decision-making in today’s fast-paced retail world.
Post a Comment